data-animation-override>
“Published in NZV8 Issue No. 65”
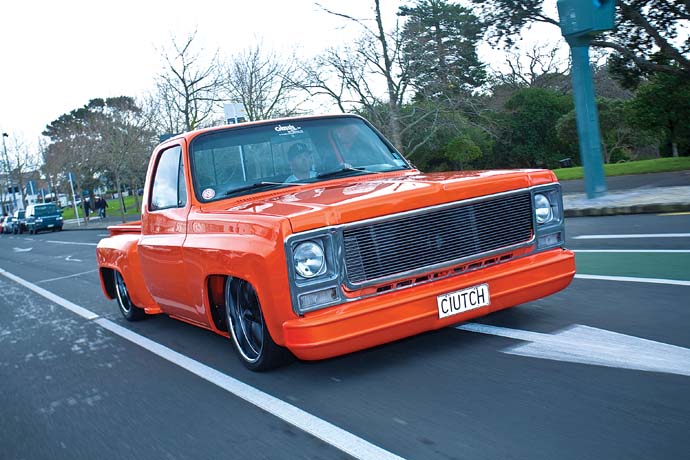
If you think the exterior of Matt Elliott’s Chev C10 is smooth, wait until you see the engine bay.
The story of Matt Elliott and his C10 is like many others. It starts off with a young guy growing up in the import scene, spending a dizzying amount of cash on cars only to lose it all when he sells them. From there he goes on to buy a V8, and decides that having previously spent so much money on mods, he may as well buy a vehicle that’s already completed. In Matt’s case, the C10 was what he found.
We actually had a look at the truck not too long after Matt bought it in 2007, and it was a pretty cool ride. It was bright orange, slammed on airbags and had a decent small block in it, so Matt looked set for endless days of cruising around Tauranga and Mount Maunganui drawing admiration from those he passed. Well, that was the plan at least.
When the transmission decided to give up, Matt didn’t think much of it and had it replaced, safe in the knowledge that these things happen and at least nothing else should go wrong. But as fate would have it, it did, and little did Matt or his now-wife Jamie know at the time, this would be the start of one seriously impressive labour of love.
Always A Catch
“After the transmission was sorted, the motor had a few issues so we decided to bring in a crate motor and drop it in,” says Matt. That sounds pretty harmless, although he mentions the engine purchase came with one catch: an engagement ring had to go with it.
It was while the engine was held up in transit that things started to snowball. “While we were waiting for it to turn up, the concept for the build changed to smooth everything out,” Matt recalls. “So we hid everything in the engine bay, shaved everything and ended up repainting every panel, and instead of just dropping the motor in we went overboard.”
Matt uses the word “overboard” here in the same way you could describe the recent oil slick in the Gulf of Mexico as a small spill. More than 1400 hours of labour have gone into making the cleanest engine bay we’ve ever seen. It’s hard to know where to start describing all the work that has gone into it, but it’s obvious Matt had some serious international inspiration, and some of the best local talent available.
The firewall was the first item to be attacked, and every protrusion was removed. The brake master cylinder has been replaced with a Wilwood item and matching pedal box hidden up under the dash. For ease of access the reservoirs are now mounted in the scuttle panel and are simpler to get to with the bonnet open. The more you look, the more you’ll find is missing from the bay, like the window wiper motor, which is also hidden away.
Best of The Best
The majority of fabrication work was taken care of by Jason Sellars at JSE Custom Fabrication, while Nakija Klaus was in charge of the sheet-metal department. Those silky smooth new inner guards may look like they’ve been created from fibreglass, but they’re handcrafted steel works of art that took more than 400 hours to create. Nakija’s metal bending skills don’t end there though; the custom radiator top panel is also his handiwork, and it nicely hides what’s usually an unsightly part of an engine bay.
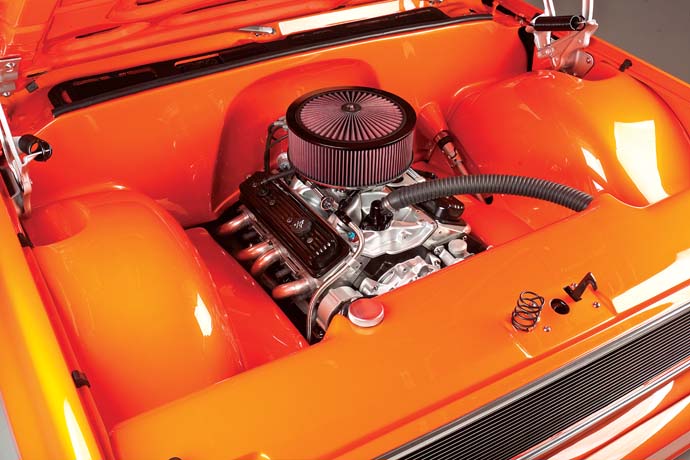
With so much time and effort going into the bay, Matt set about dressing up the GM ZZ383 crate motor once it arrived. While it may look simple, there are a few touches that generally go unseen. Details like the recessing of bolts, colour coding and a hidden power steering unit tend not to be noticed until they’re pointed out, such is the quality of the job.
Cory Abbot was called upon when it came time to wire the vehicle, and he was under strict instructions to keep the visible cabling to an absolute minimum. The job was time-consuming and resulted in no original wires remaining in the vehicle. After 200 hours of cutting, crimping and soldering, Cory’s job was complete. Not a single strand is visible, yet all the electrics work perfectly.
With the engine bay soon far beyond the standard of the rest of the truck, Matt knew he couldn’t stop there. He points out that finishing the truck cost him not just time and money, but the price of a wedding, too. Since Jamie is obviously pretty patient with him and his obsession, we think that’s probably not that bad a deal.
Same Again please
With Jason having fabbed up countless parts for the engine bay, including the custom headers, he was also enlisted to help in the tray area. Matt wanted to continue the clean theme, so the existing chequer plate tray floor was removed and the lines for a new one were marked out. Jason’s job was to create a custom drop tank, plus new mounting points for the airbag suspension components as well as the battery. Again, it’s not about what you see here but what you don’t. The new one-piece wave-shaped tray floor was skilfully rolled up and slid into place, hiding all that lies beneath.
The smoothing obsession continued to the rest of the exterior where Nakija, who at the time was working for Iron Rides, (and can now be found at Rods By Reid) once again got his welder acquainted with the truck’s body. The front repeater lights were removed along with the bumper mounting bolts, drip rails, mirrors and door handles.
With these items gone, he set about creating a custom roll pan, hidden tailgate latch, custom tail lights and a number plate light. It all sounds easy but the hours were soon clocked up in the quest for smooth perfection.
From there it was off to Willy Johnstone at High Impact Paint, who applied the House of Kolor Tangelo Pearl over a top secret base colour. It may have been orange when Matt first purchased it, but the House of Kolor paint took it to a whole new level. The depth and pearls really make the curvaceous panels of the engine bay and tray come alive under the slightest hint of sunlight to showcase the workmanship perfectly.
The Theme Continues
Although the closest the rest of the country will get to the vehicle is admiring it from afar, Matt turned his hand to the interior, which was not too shabby to begin with.
While the trim remains as it was when purchased (and it’s about the only part of the vehicle that does) the ’70s dash panel has been replaced with something far more modern. Rather than go for the simple flat-panel option to hold his newly acquired hoard of Auto Meter gauges, Matt again tested Nakija’s ability by having him sculpt another work of art. Beside the other gauges, there’s a Dakota Digital air pressure gauge to give the pressures on the suspension at all four corners whenever the key is on.
Those pressures are kept up by two compressors hidden under the tray, transmitted to the airbags via half-inch lines. Jason was responsible for creating the custom adjustable four-link rear end as well as mounting the QA1 shocks in charge of damping. Up front the stock A-arms have been modified to allow fitment of the bags, and three-inch dropped spindles were added to further reduce ride height and help with the camber correction involved in such a drop.

Matt’s happy to admit that he’s better kept out of the way when it comes to fabrication and intricate mechanical work, so he also left the fitment of Wilwood callipers and rotors both front and rear to Jason. With big 20-inch MHT rims and the possibility of 22s filling the spaces in future, Matt decided on 330mm rotors up front and 324mm items in the rear. Not content to leave anything alone, he’s had the rotors and callipers colour coded, as well as the massive rims.
Never Enough
While the fabrication work and the end result are the most impressive aspects of the build, the fact it was completed within a year is also remarkable. “It’s only 99 per cent done,” Matt reckons. “In the future I would like to boost it in some way, shorten the diff and get some 12-inch-wide rims under the back and maybe go to 22s.” Judging by what he’s done so far, we’re pretty sure that list won’t take long to complete.
If he had another shot, would Matt do anything differently? Not really, he says. “The one thing I learnt was that it pays to get the best of the best to work on your stuff. Sure, they may cost a bit more than others, but you get the best work done first time and generally on time.”
Matt’s C10 is certainly testament to that mantra.
After spending a few hours running a fine-tooth comb all over the truck, NZV8 is yet to find a single flaw. Matt reckons there are one or two but, for a perfectionist, he’s surprisingly unfazed by that.
“The truck has its imperfections,” he says, “but you need to draw the line somewhere or you will never drive your vehicles.”

Specifications
Engine: 383ci (6.3-litre) small block Chevrolet crate motor, four-bolt mains, one-piece main seal, 96.5mm (3.8-inch) stroke forged scat crank, hypereutectic 244-T5 pistons, 9.1:1 compression, billet camshaft, Edlebrock E-Tec 200 Vortec-style alloy heads, 1.5:1 roller rockers, Weiand Stealth Air Strike Vortec intake, all mounting bolts countersunk and recessed, Holley 770 street avenger carb, K&N filter, 50-litre custom stainless tank, -8 and -10 lines, Summit inline billet filter, Holley mechanical fuel pump, MSD Street Fire HEI distributor, MSD high spark replacement module with rev limiter, MSD 8.5mm leads, Jason Sellars Fabrication custom 1-5/8-inch headers, twin three-inch pipes dumping before diff, Segedins alloy radiator, 406mm fan, hidden overflow bottle, hidden wiring, custom hinges, custom Gilmer drive, shaved firewall, custom all steel inner guards, custom smoothed front cowl, remounted steering column, hidden power steering pump and lines.
Driveline: B&M Turbo 350, 2500rpm stall converter, shift kitted, Chevrolet C10 12-bolt diff, Moser Engineering 12-bolt axles, Eaton Posi Torque LSD, modified standard driveshaft, remote mounted transmission cooler
Suspension: (Front) Factory control arms modified to accept RideTech airbags, 3-inch drop spindles; (rear) RideTech adjustable triangulated four-link, Firestone airbags, bag-over-axle arrangement, QA1 Proma Star single adjustable shocks, 32mm front sway bar, 32-litre alloy air tank with custom drain, ½-inch air lines, Dakota remote control system, eight-way solenoid setup, two DC4000 compressors
Brakes: 330mm cross drilled and slotted front rotors, Wilwood GM two-pot replacement callipers front; Wilwood C10 rear disc brake kit, 324mm cross drilled and slotted rotors, Wilwood four-pot callipers and pads, custom-mounted Wilwood pedal box and hidden master cylinders, no booster
Wheels/tyres: 20×8.5-inch MHT Drive, custom painted centres, Bridgestone S-03 front tyres 255/35R20, Michelin 275/45R20 rears
Exterior: Shaved front bumper with hidden mounting points, shaved front repeaters, shaved mirrors, shaved door handles, shaved drip rails, custom rear light buckets, custom rear roll pan, custom hidden tailgate access and latch, hidden wiper motor, custom LED tail lights, custom rear number plate LED lights, tubbed rear tray, remote fill master cylinder reservoirs, House of Kolor Tangelo Pearl paint
Chassis: Custom air and fuel tank mounts, custom cross members and c-notch
Interior: Retrimmed factory seats, Momo leather steering wheel, Ididit polished adaptor, B&M Hi-Tek Street Bandit shifter, Auto Meter Sport Comp gauges, Dakota digital air pressure gauge, four corners and tank; custom steel dash panel, Ididit polished steering column with custom Borgeson telescopic shaft and joints, custom Wilwood accelerator pedal made from a Wilwood clutch pedal, S2000 engine start button, custom hood lining, Autoloc keyless entry system, fully lined with Dynamat, Alpine head unit, Pioneer component speakers
Performance: 450hp (336kW)

Owner Profile
Matthew Elliot
Car club: Low Fast Famous
Age: 34
Occupation: Area sales manager, Bay Engineers Supplies
Previously owned cars: Mazda RX-3, Ford Escort Sport, Mitsubishi Evo II
Dream car: This with a Procharger or big turbo, or a Lamborghini Gallardo or 1972 Chev C10 with a custom chassis, twin turbo LS3, 22s all round and a six-speed sequential box
Why the C10?: I had been on the look-out for a V8 vehicle for a while, saw this and thought it would be good as it was all done — little did I know! We have replaced everything in it over three years and repainted every panel.
Build time: One year solid
Length of ownership: Three years
Matt thanks: Nakija Klaus aka NKD for helping with the concept and creating all the amazing sheetmetal work and being a top bloke. Yours is next! Jason Sellars at JSE Custom Fabrication (027 449 5755) for helping with all aspects of the build and going above and beyond to get it finished. Could never have done it without you. Shannon Peake at Iron Rides, Te Puke (07 573 4464), Willy Johnstone at High Impact Paint for the amazing paint and ability to take concepts to reality (07 577 1931), Cory Abbot for all wiring work, taking the piss and more, John, Nakija and Flick at Rods By Reid (07 552 5977), Bay Engineers Supplies (07 572 9470), Dean at Landon Motorsport (027 490 3576) for the tune-up, Grant Crosby for driving the transporter to the photo shoot and all billet machining, Steven at Richards Toyota (07 862 7674) for the use of the transporter, my wife Jamie for all her support and understanding when we could not go
cruising last summer.
Words: Todd Wylie
Photos: Adam Croy